Understanding core colours and why it matters
If you inspect the wiring of an older property, you may notice that the colours of the insulation covering the conductors in the cable are different to those of cables today.
This is because the UK adopted the harmonised wiring colours outlined by the International Electrotechnical Commission (IEC) to create a standardised system for wiring. The 16th edition of the IET Wiring Regulations (Amendment 2), published in 2004, introduced the new core colour changes, and from 2006, it was mandatory for all new installations to use the standardised colours.
Why do colours matter?
Different colours are used to identify the purpose of each conductor. This is especially important in multi-core cables, such as in three-phase systems or control wiring. By quickly identifying the role of each conductor, electricians can ensure safe and accurate installations.
A standard, single-phase domestic cable such as Prysmian twin and earth, will include brown and blue coloured insulation, typically used as live and neutral, with an uninsulated or bare copper as circuit protective conductor (CPC), ideally sleeved green/yellow at joints or terminations.
It is worth mentioning that control cables such as the fire-resistant Prysmian FP500, feature numbered cores that are all the same neutral colour with a different number on each core. For this five-core cable, it’s 1-5 inclusive. This type of cable is designed as a control cable rather than power cable so all cores could carry current and voltage.
In three-phase circuits, multiple core colours are used, depending upon circuit design brown for line 1 (L1), black for line 2 (L2), grey for line 3 (L3), blue for neutral and green/yellow for earth. However, similarly to the cores in single-phase circuits, this was not always the case.
A brief history of core colours
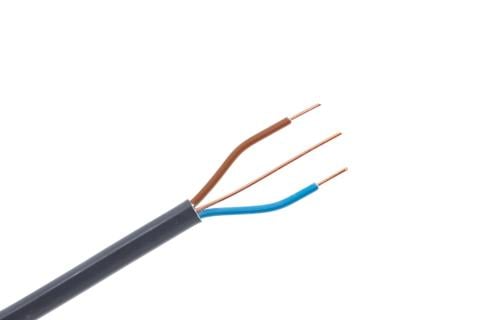
The earliest conductors were uninsulated and relied upon air to prevent failure, and when insulation was introduced, it was paper impregnated with insulating oils and waxes...Before 2006, the UK used the following colour-coded system for single phase circuits: red for live, black for neutral, and green/yellow for earth. But when did we start using colours?
Core colour insulation was first introduced in 1916. The 7th Edition of the IET Wiring Rules and Regulation 51, back then called IEE, provided recommendations for identifying conductors by colour. However, the 13th Edition of the Wiring Regulations published in 1955, saw the first use of a table for colour identification, stating red to be used for live, black for neutral and green for earth.
The earth conductor was just green coloured until 1976. Following the amendments to BS 7671 (14th edition), earth conductors switched to green/yellow. The use of green on its own was phased out by 1977.
The colour combination for earth conductors is quite specific. In accordance with the 15th edition of the Wiring Regulations, one colour must occupy not less than 30% and not more than 70% of the total visible surface area, with the remaining part covered by the second colour. In practise, the split of colours is much more likely to be 50/50. This helps to prevent rejects in product sampling from being too close to the limits.
However, it is more common to see these conductors completely coloured in yellow with a green stripe on the surface. Thought to be the higher cost of the masterbatch colour, which influences the ratio of yellow and green. Yellow is lower cost.
The core colours for conductors used in three-phase circuits before 2006, went as follows; red for L1, yellow for L2, blue for L3, black for neutral and green/yellow for the earth conductor.
Why did the colours change?
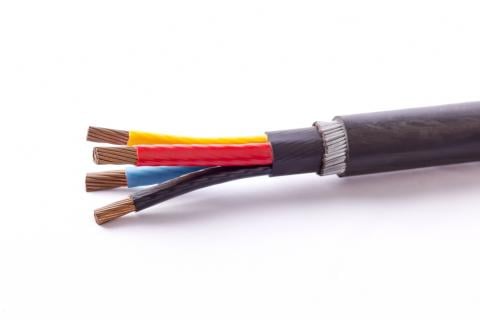
Although it was a nationally recognised colour-coded system, it was not a familiar one in Europe. The UK harmonised the wiring colours to meet the European Standards, primarily for safety. In addition to reducing confusion and improving safety, this created a standardised system for wiring. Harmonising the conductor colours made it easier to move electrical equipment and components between the UK and other European countries. This was especially important for electrical professionals who were working on different projects in different regions.
Between April 2004 and March 2006, as the new colours came into effect, both old and new colour systems were allowed in the UK. However, they could not be used in the same installation. From April 2006, the old colours could no longer be used in new installations or modifications.
Understanding core colours in electrical wiring is essential for ensuring safety and compliance across all installations. Prysmian supports this by carefully selecting high-performance polymers in the production of our PVC and XLPE cables. The coloured layer (the masterbatch colour) is more expensive than the base insulation, therefore its correct application is vital. If the colour is not correctly applied, the skin can separate, increasing the risk of arching and electric shock.
Poor bonding can offer some cable manufacturers a shortcut in bringing costs down during manufacturing. Prysmian, however, is committed to delivering high-quality, fully compliant products such as our twin and earth cables, ensuring both performance and peace of mind for installers. If you have any questions on cable cores, contact us today.