A guide to cable stranding
Whilst all cable conductors are made from metal, not all of them are made in the same way. Some conductors are a single, solid wire of copper or aluminium, while others are made up of individual wires through a process called “stranding”. This involves twisting the wires together to form a single conductor. Stranded conductors typically comprise 7, 13, 19, 27, or more individual wires. But what is the purpose of stranding cable and how is it made?
Why are cables stranded?
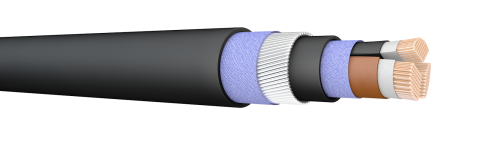
Cables are stranded mainly to enhance pliability, durability and reliability. A cable with a single, solid conductor can be difficult to install or route through conduits and around bends or buried in ground. Using stranded conductors, however, offers greater pliability whilst still conducting electricity efficiently. This is essential in for cables in buildings.
It is worth noting that having greater pliability does not necessarily mean that the cable is flexible. Cables used in fixed installations—such as Prysmian FP200 Gold or twin & earth cable—can be bent or shaped during installation, however, unlike the flexible cables used to connect appliances such as irons or hairdryers to the fixed wiring circuit, they are not designed to be repeatedly moved or bent without risk of damage.
A stranded cable is also more durable, thanks to its pliability. This means less risk of breakage from vibration or constant movement when using portable devices.
BS 7671 (IET Wiring Regulations) and BS EN 60228: Conductors of insulated cables, provide guidance on how stranded cables should be manufactured and installed. Stranded cables typically fall under two categories in the UK: Class 2 and Class 5.
Class 2: stranded conductors – used mainly in fixed wiring
Class 5: flexible and extra-flexible stranded conductors – typically used where flexibility is vital, such as portable appliances and moving machinery
How are stranded cables made?
Cable stranding is a complex manufacturing process. In Prysmian factories, for example, fine individual wires are drawn down to the required size, depending on which final conductor size is needed, from a 9mm diameter copper rod. (The copper rod is delivered daily in five-tonne packs to every Prysmian factory. Immediately after drawing, the wire is annealed to allow recrystallisation of the copper, which relaxes the internal structure to make it more pliable and less brittle. Following this, the wires are helically applied (twisted) in a right-hand lay (clockwise direction).
It is worth mentioning that the wires twisted around a central strand need to be longer than the central strand itself. For example, if the central strand is 1000m, then the strands twisted around it will need to be longer to ensure it completes the required length – otherwise the wires will run out during manufacture!
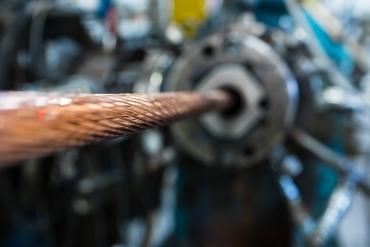
The normal result is a circular copper stranded conductor; however, they can also be circular compacted or sector-shaped conductors. The circular compacted conductor—as the name suggests—is a type of stranded cable where individual wires are shaped and compressed together to form a more compact, rounder and smoother conductor. This reduces air gaps between the strands, leading to a smaller conductor diameter.
In some cases, such as large sizes of Prysmian SWA power cable or Prysmian FP600s, where the nominal cross section of the conductor is between 50-400 mm², the conductors are sector-shaped. This means the conductors are arranged in a shape resembling a sector of a circle – like slices of pie. So, a four-core cable would have four, quarter-shaped or 90° conductors, a three-core cable would have three, 120° shaped conductors and a two-core cable would have two, 180° shaped cores. When these sectors are brought together also in a helix, they form a full circle in the cable. This is to allow for a larger cross-sectional area of the conductor without wasting space that would mean more cable fillers, larger-sized cable fixings, glands and containment.
After stranding, the conductors are typically insulated with polyvinyl chloride (PVC), or cross-linked polyethylene (XLPE) and then go on to the next stage of cable manufacture.
Are there any issues with stranded cables?
In a worst-case scenario, such as a flood, stranded cables can be more prone to water penetration than solid conductors unless suitably protected, which can lead to electrical system issues. This is due to the tiny gaps between the strands. Should the worst happen, the cables should be thoroughly tested and checked for potential damage. For large, high voltage distribution and transmission network cables such as windfarms, “water blocking” tapes form part of stranded conductor design. Should the cable be damaged long after installation then any water ingress can be slowed and reduce the size of repair section required.
Because more operations happen when manufacturing a stranded conductor, Prysmian measures the conductivity before and after each process to ensure is meets the specification.
Aluminium stranded cable
We have been mainly talking copper stranded cables, but what about aluminium stranded cable? Essentially, aluminium cables are stranded in the same way as copper, however they are extensively used in overhead power lines and some large-scale distribution and transmission systems.
Overall, stranded conductors offer enhanced pliability, durability, and ease of installation in both fixed wiring and dynamic applications. Understanding the purpose of stranded cables and how they are made, helps to ensure the right choice is made for each electrical installation.
If you have any questions about cable stranding, why not contact us today?